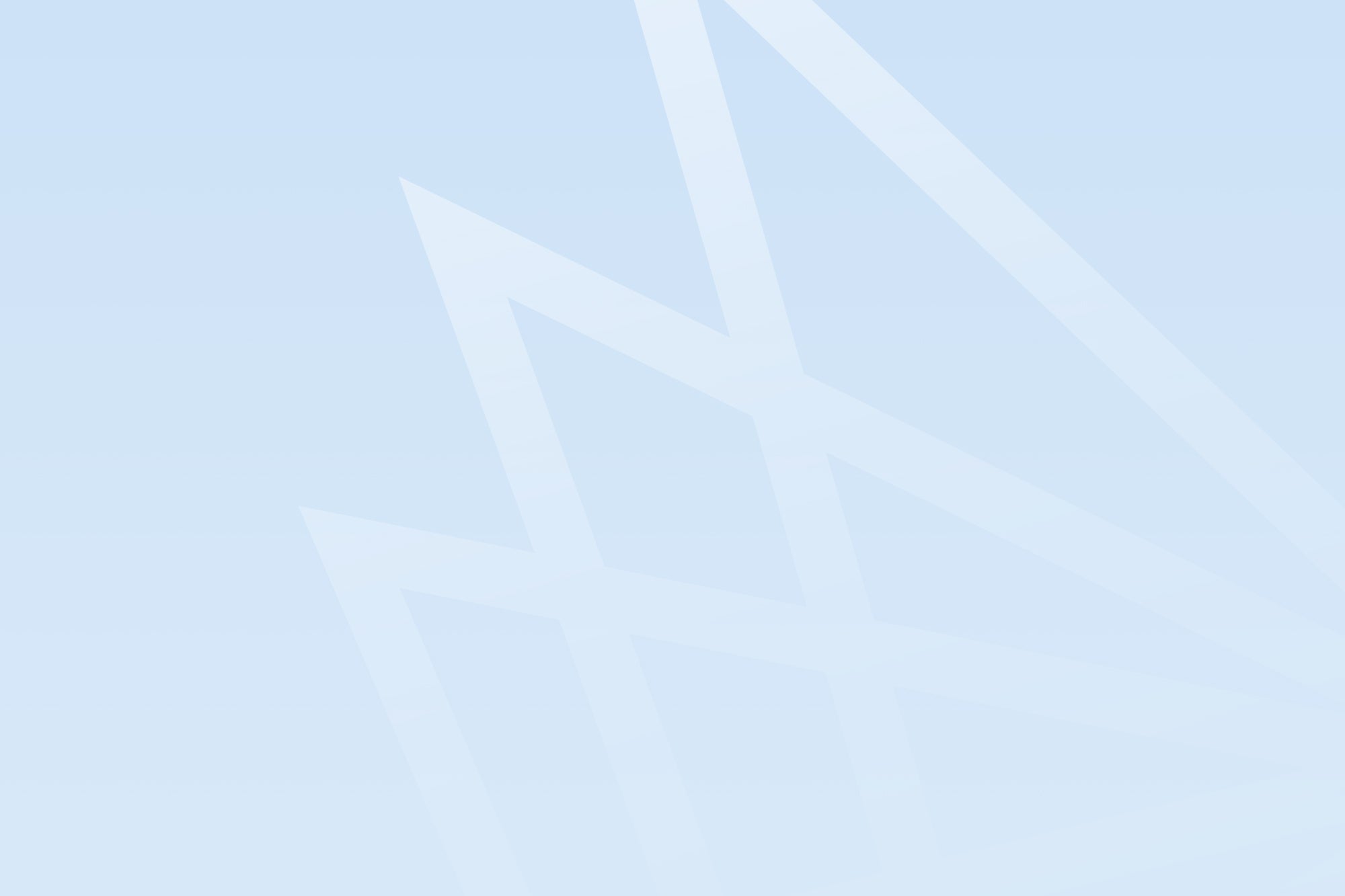
Costly MRI Malfunctions Eliminated by ECRI
Problem
Magnetic resonance imaging (MRI) scans are utilized often in healthcare; in the United States alone, more than 40 million MRIs are performed annually. But what happens when this trusted and well-utilized technology suddenly becomes unreliable?
One large health system in the Midwest encountered this issue when one of their MRIs quenched twice within six months. Quenching refers to the sudden loss of absolute zero temperature in the MRI’s magnet coils, which results in a loss of superconductivity, and therefore the loss of the magnetic field. This causes a sudden and rapid heating, which boils the liquid helium converting it to gas. If the helium-venting equipment is functioning, the helium will be safely dispelled outside of the building. If it is not, the MRI room is likely to rapidly fill with helium, displacing all the oxygen in the room. One unplanned quench puts staff and patients at risk for asphyxia, hypothermia and ruptured eardrums, and it can cost a hospital at least $80,000 in repairs and $10,000 to $15,000 per day in lost revenue. MRI repair times can take up to one to two months.
Solution
The health system had already experienced two quenches followed by months of
MRI downtime as the machine was being rebuilt, so they knew they needed outside assistance. Through their Risk Retention Group (RRG), the health system is a member of ECRI and the Institute for Safe Medication Practices PSO. Quickly, they reached out to their PSO advisor for guidance. Working with the ECRI device and evaluation experts, the PSO advisor was able to help the client identify potential causes of the quench.
Based on an assessment, the ECRI device expert quickly provided information on technical specifications that allowed for better communication of operational needs between the vendor and the health system. The support from the PSO promoted better ongoing communication, and allowed the development and implementation of new policies and protocols to train staff on how to handle a quench, and to protect patients and staff if one did occur. This included building training, ensuring the exits were clear, that doors opened out, and that staff were regularly trained for emergency situations.
As part of a comprehensive evaluation, ECRI identified gaps in the MRI maintenance process. ECRI’s device experts closed those gaps by managing the process changes with the MRI vendor. ECRI helped the member and vendor establish and communicate maintenance standards, create a regular monitoring schedule, and negotiate vendor responsibility for tech qualifications.
Result
With ECRI’s assistance, the RRG member health system was prepared to prevent future accidental MRI quenches. Working with ECRI potentially saved the member over $1 million by preventing future MRI failures, by changing maintenance and safety protocols to prevent the risk. In addition, the changes implemented made staff more willing to speak up about other concerns and resolve risks before an event occurred.