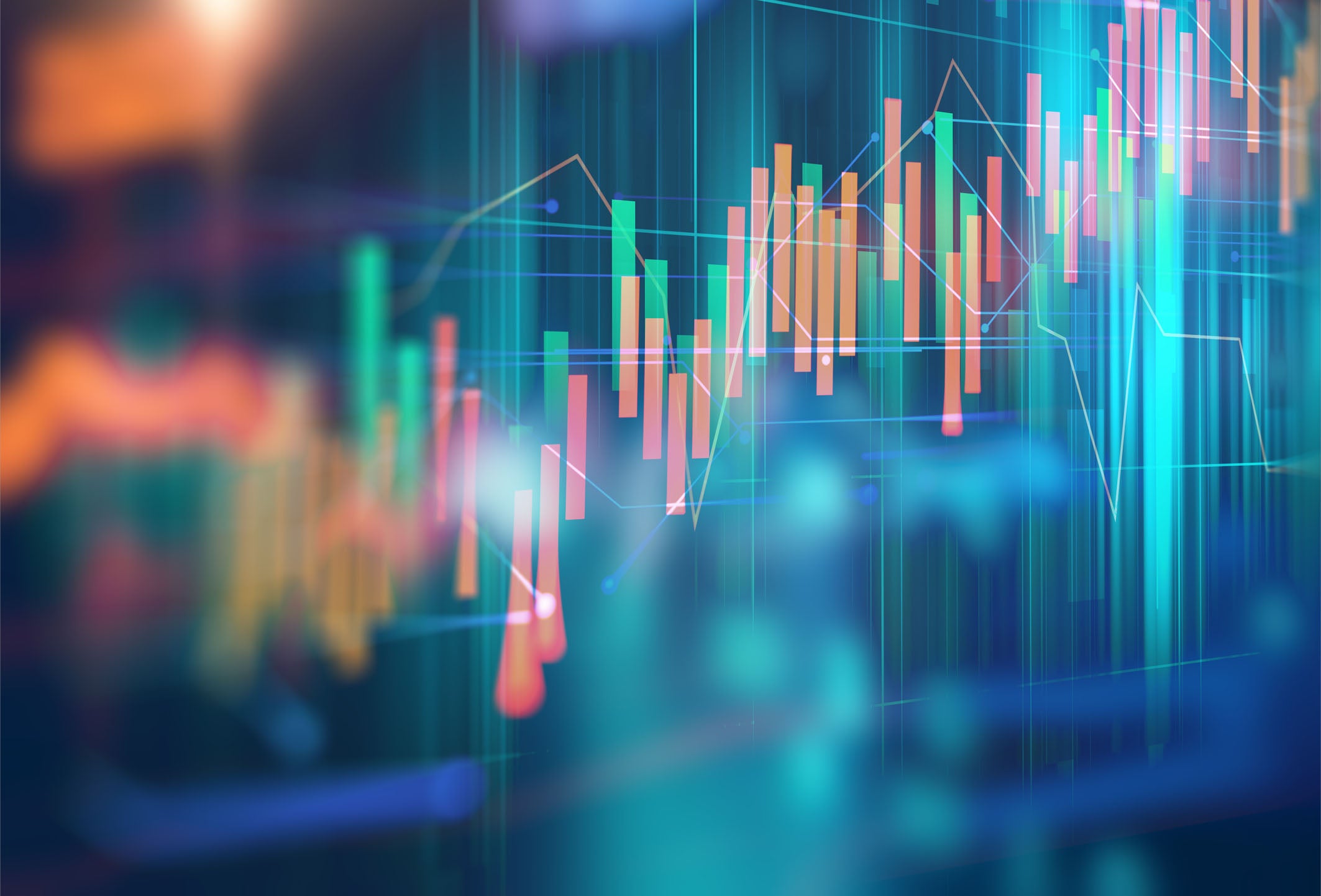
Use Inventory Standardization to Improve Your Safety and Recall Alerts Program
We’ve all heard the idiom that one should “compare apples to apples; not apples to oranges. But what if you are not calling all of your apples by the name apple, or oranges by the name orange?
Or, here’s another way to think about it: Having mismatched data is like having an unorganized closet—you can’t find anything when you need it, you waste time searching, lose money in new purchases, and the closet gets messier as time goes on.
When managing hospital equipment inventory, lack of data standardization poses serious issues. Without standardization of manufacturers, product names, and details, you don’t have a clear picture of what is in your inventory or the information you need to react to safety and recall alerts in a timely manner. This can lead to costly mistakes and affect your ability to deliver quality patient care.
One bad apple: dirty data
Data that is incorrect is called “dirty data." Dirty data in hospital inventory can be incorrect for a number of reasons; it can contain duplicates, or be incomplete or outdated. Maybe it has errors such as misspelled names or incorrect information, or have the incorrect or outdated manufacturer listed. It’s a common issue as organizations merge or purchase new inventory.
Whatever the issues, they are roadblocks to making data-driven decisions for managing your inventory and your safety and recall alerts program impacting your responses, predictive replacement planning, and even cybersecurity updates. However, standardizing inventory is a continuous challenge—and something many vendors can’t provide.
And dirty data costs you more than just time; one estimate cites dirty data as a $600 billion annual problem in the United States alone.
Creating order: Inventory Standardization
Keep in mind that managing data should be everyone’s responsibility. Everyone from the CEO on down should play a role in creating data quality. Next, seek out a skilled partner that can help you assess your data and clean it up using a thorough process that prevents repeat mistakes. Finding that partner is the best way to standardize your data - and ensure it stays that way.
ECRI’s Inventory Standardization organizes the various different names, manufacturers and models in your inventory on a continual basis, keeping your inventory organized and up-to-date. ECRI's process entails reviewing your medical equipment inventory from your Computerized Maintenance Management System, assigning standard manufacturer, product or model names, as well as the appropriate device classification to reduce variability in your inventory. This enables you to match “apples to apples,” saving you time and money, and increasing decision-making ability and confidence.
Want to learn more? Visit us at https://www.ecri.org/solutions/alerts-workflow/