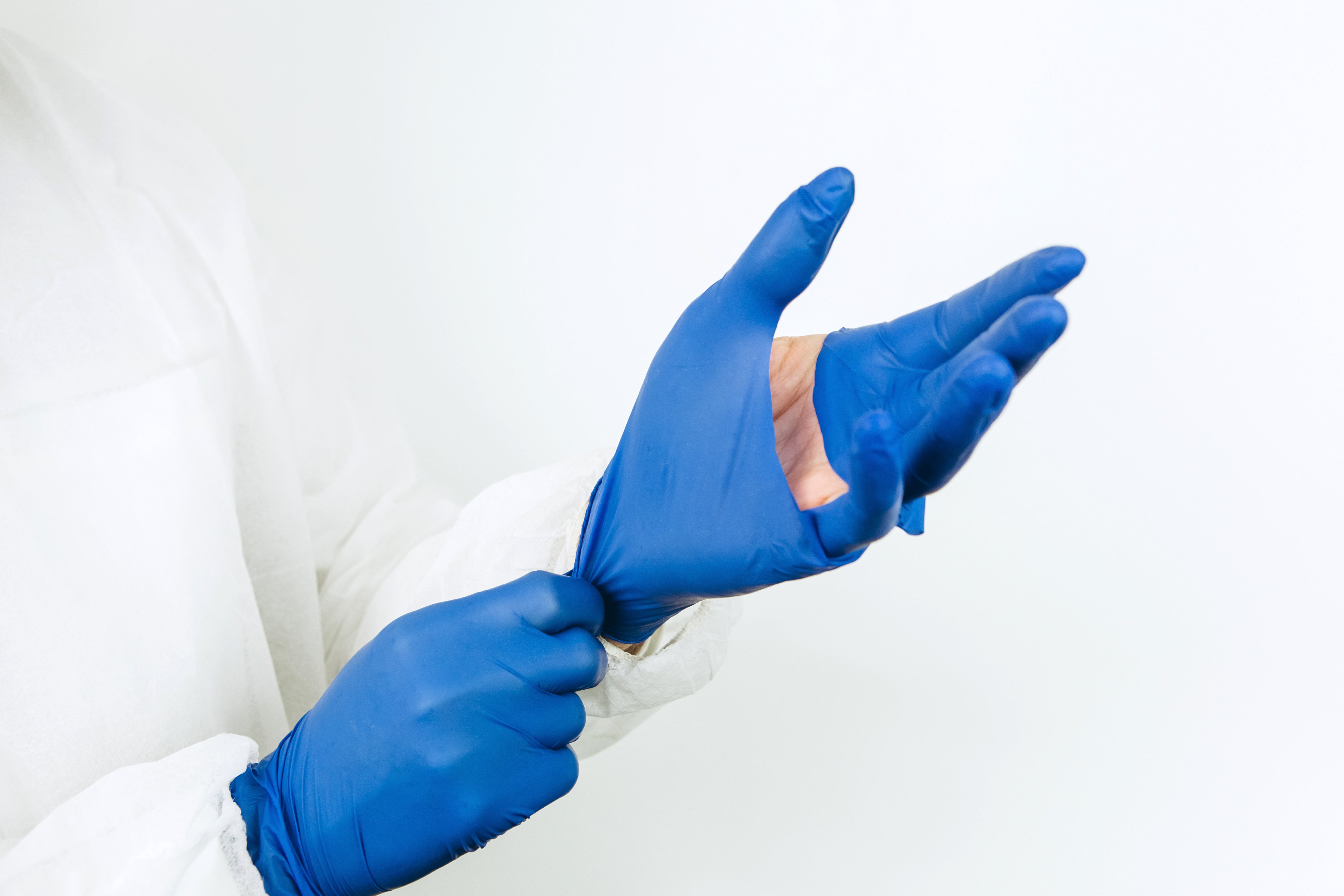
Combating Substandard and Counterfeit Medical Devices
Healthcare organizations are increasingly vulnerable to the dangers of substandard and counterfeit medical devices and supplies. Ranked as the fourth-highest hazard in ECRI's Top 10 Healthcare Technology Hazards for 2025, substandard devices and supplies pose significant threats to patient safety, disrupt healthcare operations, and contribute to rising costs. Proactive vigilance and robust measures are essential to address this critical issue.
Several recent, high-profile incidents highlight the growing prevalence of substandard or fraudulent medical products in the healthcare supply chain.
Faulty Syringes: A series of FDA safety communications issued from 2023-2024 stated that plastic syringes manufactured in China could be prone to failure. The issue has the potential to affect over one billion products in US healthcare facilities. The dangers of faulty syringes include having inaccurate measurement markings, malfunctioning plungers, or defects that introduce residue or foreign particles into the syringe barrels.
Isolation Gown Quality Issues: Testing of disposable isolation gowns continues to reveal significant quality concerns, with some products distributed over the past four years failing to meet safety standards. These gowns may not provide adequate protection against bloodborne pathogens, body fluids, or other contaminants, which could increase the risk of infections among healthcare workers and patients.
Counterfeit Diabetes Testing Devices: There has been a rise in counterfeit diabetes testing devices being sold through online marketplaces and unauthorized distributors. These counterfeit devices may cause faulty readings that can lead to dangerous outcomes such as diabetic ketoacidosis, cardiovascular events, or coma.
Counterfeit Infusion Pump Batteries: Counterfeit batteries for infusion pumps have also entered the market, posing risks of imprecise medication delivery, overheating, leaking, and other significant hazards.
Main Challenges in Tackling Substandard Devices and Supplies
Strengthening the integrity of the healthcare supply chain is critical to ensure the delivery of safe and effective medical equipment. However, several barriers must be addressed to effectively combat these risks.
- Complex Global Supply Chains: The vast network of suppliers, each with varying regulatory standards, makes it difficult to guarantee product integrity. During shortages, facilities may resort to underregulated and non-vetted third-party vendors, increasing the risk of receiving counterfeit products.
- Limited Supplier Visibility: Healthcare organizations often lack transparency in their suppliers' practices, making it difficult to verify the legitimacy and quality of the devices and supplies being purchased.
- Lack of Reporting: Tracking and reporting defective devices, even those that do not harm patients, is crucial for identifying trends. Failure to report these defects to internal Materials Management and suppliers means no investigations or corrective actions.
-
Delayed Safety Notices: Without advanced monitoring systems, healthcare organizations may struggle to quickly identify defective or substandard products in their inventory. This delay can lead to further complications and safety risks.
Inconsistent Regulatory Oversight - Regulatory bodies vary in their enforcement mechanisms, and some regions lack the resources to monitor supplier quality effectively or to bar entry of counterfeit products, leaving gaps in the supply chain that may allow faulty devices to enter the market.
Solutions to Overcome These Challenges
To address these challenges and strengthen healthcare supply chains, organizations should adopt several key strategies.
-
Rigorous Supplier Evaluation
- Implement a comprehensive supplier vetting process, ensuring suppliers meet quality standards and regulatory certifications.
- If possible, purchase all devices and products directly from the manufacturer or trusted distributors, rather than from consumer e-commerce websites.
- Conduct regular audits to verify ongoing compliance with industry norms.
-
Product Testing Before Procurement
- Establish thorough testing protocols for all new products, especially from new or unfamiliar suppliers, including soliciting feedback from facility end-users (e.g. clinicians and nurses).
- Partner with independent testing organizations to validate product safety and performance before purchase.
-
Supply Chain Integrity and Traceability
- Use tamper-evident seals, overwraps, and security labels that clearly indicate if a product has been tampered with.
- Ensure traceability through proper labeling and barcode scanning/serial number checks or use advance technological tracking (e.g. RFID) to ensure transparency.
-
Incident Response Protocol and Staff Training
- Work with appropriate groups in your organization to establish processes for reporting defective products, both internally (e.g., to materials management) and externally (e.g., to the manufacturer, your patient safety organization, FDA, and ECRI), as circumstances warrant.
- Regularly train staff on these protocols to ensure quick and effective responses in case of incidents.
-
Staff Awareness and Education
- Educate healthcare staff on recognizing counterfeit or substandard products by identifying warning signs such as suspicious packaging or unusually low prices.
- Keep staff informed about emerging trends in counterfeit devices and encourage continuous learning.
-
Advocating for Industry Standards
- Engage with industry groups and regulatory bodies to push for stronger regulations and more stringent enforcement of quality standards.
- Support initiatives aimed at improving manufacturing controls and restricting unauthorized distribution of medical devices.
Additional Strategies
In addition to these strategies, healthcare organizations can leverage external expertise to further enhance their risk management.
Incident Reporting Systems: Establish frameworks for reporting substandard products, enabling quick action, and drawing on external networks to track and address risks.
Regulatory Compliance Advisors: Collaborate with experts to stay up to date with evolving regulations and ensure organizational practices align with current standards.
Third-party Assessors: Partner with independent evaluators who specialize in product quality assessments to identify potential risks before products are introduced into the supply chain.
Conclusion
By addressing these barriers through comprehensive strategies such as rigorous supplier controls, enhanced traceability, and increased staff awareness, healthcare organizations can significantly reduce the risks posed by substandard and counterfeit devices. This proactive approach will help safeguard patient safety, maintain the integrity of healthcare operations, and ensure the reliability of the supply chain, ultimately securing a safer and more resilient healthcare environment.
Learn how ECRI can support your purchasing decisions with objective, evidence-based insight, supported by independent laboratory testing, specification recommendations, and real-world user feedback.